Las cajas de plástico son un tipo de equipo logístico utilizado para la distribución de productos de moldeo por inyección de plástico. Generalmente, se fabrican con HDPE (polietileno de alta densidad y baja presión) de alto impacto y PP (polipropileno) como materias primas. Al seleccionarlas, se deben considerar siete factores: contracción, fluidez, cristalinidad, plásticos termosensibles y fácilmente hidrolizables, agrietamiento por tensión y fractura por fusión, propiedades térmicas y velocidad de enfriamiento, higroscopicidad, etc.
El concepto de caja de plástico
Las cajas de plástico se suelen llamar: cajas de plástico, cajas de plástico, cajas de plástico giratorias, cestas de plástico, cestas de plástico giratorias y cestas de plástico.
La caja de plástico es unaProductos de moldeo por inyecciónProductos de equipamiento logístico para la rotación de plástico
Material de caja de plástico
Está fabricado con HDPE (polietileno de alta densidad y baja presión) de alta resistencia al impacto y PP (polipropileno) como materias primas para el moldeo por inyección. La mayoría de las cajas se fabrican mediante moldeo por inyección de una sola vez, y algunas cajas de plástico también incluyen tapas (planas y abatibles). Algunas cajas logísticas son plegables, lo que reduce el volumen de almacenamiento cuando están vacías y los costos logísticos.
Siete factores a considerar en el proceso de moldeo por inyección de plástico
Contracción
Formas y cálculos de la contracción del moldeo de termoplásticos Como se mencionó anteriormente, los factores que afectan la contracción del moldeo de termoplásticos son los siguientes:
1.1 Tipos de plástico. Durante el proceso de moldeo de termoplásticos, se producen cambios de volumen causados por la cristalización, fuertes tensiones internas, grandes tensiones residuales congeladas en las piezas de plástico, una fuerte orientación molecular y otros factores. Por lo tanto, en comparación con los plásticos termoestables, su tasa de contracción es mayor, su rango de contracción es más amplio y su direccionalidad es evidente. Además, la contracción tras el moldeo, el recocido o el tratamiento de ajuste de humedad suele ser mayor que la de los plásticos termoestables.
1.2 Características de las piezas de plástico. Cuando el material fundido entra en contacto con la superficie de la cavidad durante el moldeo, la capa exterior se enfría inmediatamente para formar una carcasa sólida de baja densidad. Debido a la baja conductividad térmica de los plásticos, la capa interior de la pieza se enfría lentamente para formar una capa sólida de alta densidad con una gran contracción. Por lo tanto, cuanto más gruesa sea la pared, más lento será el enfriamiento, y cuanto más gruesa sea la capa de alta densidad, mayor será la contracción. Además, la presencia o ausencia de insertos, así como su disposición y número, afectan directamente la dirección del flujo de material, la distribución de la densidad y la resistencia a la contracción, entre otros factores. Por lo tanto, las características de las piezas de plástico tienen un mayor impacto en el tamaño y la dirección de la contracción.
1.3 La forma, el tamaño y la distribución del puerto de alimentación afectan directamente la dirección del flujo de material, la distribución de la densidad, el mantenimiento de la presión, la compensación de la contracción y el tiempo de moldeo. Los puertos de alimentación directos y los puertos de alimentación con secciones transversales grandes (especialmente las más gruesas) presentan una contracción baja, pero una direccionalidad alta, mientras que los puertos de alimentación con anchos amplios y longitudes cortas presentan una direccionalidad baja. Los puertos de alimentación cercanos al puerto de alimentación o paralelos a la dirección del flujo de material presentan una contracción alta.
1.4 Condiciones de moldeo. Cuando la temperatura del molde es alta, el material fundido se enfría lentamente, presenta alta densidad y se contrae considerablemente. Especialmente en materiales cristalinos, la contracción es mayor debido a la alta cristalinidad y al gran cambio de volumen. La distribución de la temperatura del molde también está relacionada con el enfriamiento interno y externo de la pieza de plástico y la uniformidad de la densidad, lo que afecta directamente la magnitud de la contracción y la direccionalidad de cada pieza. Además, la presión y el tiempo de mantenimiento también influyen considerablemente en la contracción. La contracción es pequeña, pero la direccionalidad es grande cuando la presión es alta y el tiempo es largo. La presión de inyección es alta, la diferencia de viscosidad del material fundido es pequeña, la tensión cortante entre capas es pequeña y el rebote elástico después del desmoldeo es grande, por lo que la contracción también se puede reducir adecuadamente. Si la temperatura del material es alta y la contracción es grande, pero la direccionalidad es pequeña. Por lo tanto, ajustar la temperatura del molde, la presión, la velocidad de inyección, el tiempo de enfriamiento y otros factores durante el moldeo también puede modificar adecuadamente la contracción de la pieza de plástico.
Al diseñar el molde, la tasa de contracción de cada pieza de plástico se determina en función del rango de contracción de diversos plásticos, el espesor y la forma de la pared, el tamaño y la distribución del puerto de alimentación, y el tamaño de la cavidad. Para piezas de plástico de alta precisión, cuando la tasa de contracción es difícil de calcular, generalmente se utiliza el siguiente método para diseñar el molde:
① Tome una tasa de contracción menor para el diámetro exterior de la pieza de plástico y una tasa de contracción mayor para el diámetro interior para dejar espacio para la corrección después de la prueba del molde.
② Molde de prueba para determinar la forma, el tamaño y las condiciones de moldeo del sistema de vertido.
③ Determinar los cambios dimensionales de las piezas plásticas a post-procesar (la medición debe realizarse 24 horas después del desmoldeo).
4.Modifique el molde según la situación de contracción real.
5. Pruebe el molde nuevamente y cambie adecuadamente las condiciones del proceso para corregir ligeramente el valor de contracción para cumplir con los requisitos de la pieza de plástico.
fluidez
2.1 La fluidez de los termoplásticos puede analizarse generalmente a partir de una serie de índices como el peso molecular, el índice de fusión, la longitud de flujo en espiral de Arquímedes, la viscosidad aparente y la relación de flujo (longitud de flujo/espesor de pared de la pieza de plástico). Un peso molecular bajo, una distribución amplia del peso molecular, una estructura molecular irregular, un índice de fusión alto, una longitud de flujo en espiral larga, una viscosidad aparente baja y una relación de flujo alta indican una buena fluidez. En el caso de los plásticos del mismo nombre, deben revisarse sus instrucciones para determinar si su fluidez es adecuada para el moldeo por inyección. La fluidez de los plásticos de uso común puede dividirse, a grandes rasgos, en tres categorías según los requisitos de diseño del molde:
① Buena fluidez PA, PE, PS, PP, CA, poli (4) metilpenteno;
② Resinas de serie de poliestireno de fluidez media (como ABS, AS), PMMA, POM, éter de polifenileno;
③Baja fluidez: PC, PVC duro, éter de polifenileno, polisulfona, poliarilsulfona, fluoroplásticos.
2.2 La fluidez de diversos plásticos también varía debido a diversos factores de moldeo. Los principales factores que influyen son los siguientes:
① Temperatura: Cuanto mayor sea la temperatura del material, mayor será la fluidez. Sin embargo, los distintos plásticos también presentan diferencias. La fluidez del PS (especialmente resistente a impactos y con alto MFR), PP, PA, PMMA, poliestireno modificado (como ABS, AS), PC, CA y otros plásticos varía considerablemente con la temperatura. En el caso del PE y el POM, el aumento o la disminución de la temperatura tiene poco efecto en su fluidez. Por lo tanto, el primero debe ajustarse para controlar la fluidez durante el moldeo.
② A medida que aumenta la presión de inyección, el material fundido está sujeto a un mayor cizallamiento y aumenta la fluidez, especialmente el PE y el POM son más sensibles, por lo que es aconsejable ajustar la presión de inyección para controlar la fluidez durante el moldeo.
③ La forma, el tamaño, la disposición, el diseño del sistema de refrigeración, la resistencia al flujo de la masa fundida (como el acabado superficial del molde, el espesor de la sección del canal del material, la forma de la cavidad y el sistema de escape) y otros factores de la estructura del molde afectan directamente la fluidez real de la masa fundida en la cavidad. Cualquier factor que provoque una disminución de la temperatura de la masa fundida y un aumento de su resistencia a la fluidez reducirá su fluidez. Al diseñar el molde, se debe seleccionar una estructura adecuada en función de la fluidez del plástico utilizado. Durante el moldeo, también se pueden controlar la temperatura del material, la temperatura del molde, la presión de inyección, la velocidad de inyección y otros factores para ajustar adecuadamente la situación del llenado según las necesidades del moldeo.
Cristalinidad
Los plásticos termoplásticos se pueden dividir en dos categorías: plásticos cristalinos y plásticos no cristalinos (también conocidos como amorfos) según muestren cristalización durante la condensación.
El llamado fenómeno de cristalización se refiere al fenómeno de que cuando el plástico pasa de un estado fundido a un estado condensado, las moléculas dejan de moverse libremente y quedan ligeramente fijas en su posición, y existe una tendencia a que las moléculas se organicen en un patrón regular.
El estándar de apariencia para distinguir estos dos tipos de plásticos se determina por la transparencia de las piezas de plástico de paredes gruesas. Generalmente, los materiales cristalinos son opacos o translúcidos (como el POM, etc.), y los amorfos son transparentes (como el PMMA, etc.). Sin embargo, existen excepciones, como el poli(4)metilpenteno, que es un plástico cristalino pero de alta transparencia, y el ABS, que es un material amorfo pero no transparente.
Al diseñar moldes y seleccionar máquinas de moldeo por inyección, se deben tener en cuenta los siguientes requisitos y precauciones para los plásticos cristalinos:
① El calor necesario para elevar la temperatura del material a la temperatura de moldeo es grande, por lo que se deben utilizar equipos con gran capacidad de plastificación.
② Durante el enfriamiento y la recuperación se libera una gran cantidad de calor, por lo que debe enfriarse por completo.
③ La diferencia de gravedad específica entre el estado fundido y el estado sólido es grande, la contracción de moldeo es grande y es propenso a aparecer agujeros de contracción y agujeros de aire.
④ Enfriamiento rápido, baja cristalinidad, baja contracción y alta transparencia. La cristalinidad está relacionada con el espesor de la pared de la pieza de plástico. Una pared gruesa implica enfriamiento lento, alta cristalinidad, alta contracción y buenas propiedades físicas. Por lo tanto, la temperatura del molde de los materiales cristalinos debe controlarse según sea necesario.
⑤ Anisotropía significativa y gran tensión interna. Las moléculas no cristalizadas tras el desmoldeo tienden a seguir cristalizándose, presentan un desequilibrio energético y son propensas a deformarse y deformarse.
⑥ El rango de temperatura de cristalización es estrecho, lo que puede provocar que el material no fundido no se inyecte en el molde o que bloquee el puerto de alimentación.
Plásticos sensibles al calor y plásticos fácilmente hidrolizados
4.1 La termosensibilidad se refiere a la sensibilidad térmica de algunos plásticos. Cuando la temperatura del material aumenta, se decolora, degrada y descompone fácilmente si se calienta durante largos periodos a altas temperaturas o si la sección transversal del puerto de alimentación es demasiado pequeña, lo que provoca un gran efecto de cizallamiento. Los plásticos con esta característica se denominan termosensibles, como el PVC duro, el cloruro de polivinilideno, el copolímero de acetato de vinilo, el POM y el politrifluorocloroetileno. Los plásticos termosensibles producen monómeros, gases, sólidos y otros subproductos durante su descomposición. En particular, algunos gases de descomposición son irritantes, corrosivos o tóxicos para el cuerpo humano, los equipos y los moldes. Por lo tanto, se debe prestar atención al diseño del molde, la selección de las máquinas de moldeo por inyección y el proceso de moldeo. Se deben seleccionar máquinas de moldeo por inyección de tornillo, la sección transversal del sistema de vertido debe ser grande, el molde y el cilindro deben estar cromados y no debe haber estancamiento de materiales en las esquinas. La temperatura de moldeo debe controlarse estrictamente y se deben agregar estabilizadores al plástico para debilitar sus propiedades termosensibles.
4.2 Algunos plásticos (como el PC) se descomponen a altas temperaturas y presiones, incluso si contienen una pequeña cantidad de agua. Esta propiedad se denomina hidrólisis y requiere calentamiento y secado previos.
Agrietamiento por tensión y fractura por fusión
5.1 Algunos plásticos son sensibles a la tensión y propensos a la tensión interna durante el moldeo, además de ser frágiles y fáciles de agrietar. Las piezas de plástico se agrietan bajo la acción de fuerzas externas o disolventes. Por ello, además de añadir aditivos a las materias primas para mejorar la resistencia al agrietamiento, se debe prestar atención al secado de las mismas y seleccionar condiciones de moldeo adecuadas para reducir la tensión interna y aumentar la resistencia al agrietamiento. Se deben seleccionar piezas de plástico con formas adecuadas y no se deben utilizar medidas como insertos para minimizar la concentración de tensiones. Al diseñar el molde, se debe aumentar la pendiente de desmoldeo y seleccionar puertos de alimentación y mecanismos de expulsión adecuados. Durante el moldeo, la temperatura del material, la temperatura del molde, la presión de inyección y el tiempo de enfriamiento deben ajustarse adecuadamente para evitar el desmoldeo cuando las piezas de plástico están demasiado frías y frágiles. Tras el moldeo, las piezas de plástico también deben someterse a un posprocesamiento para mejorar la resistencia al agrietamiento, eliminar la tensión interna y evitar el contacto con disolventes.
5.2 Cuando una masa fundida de polímero con un determinado índice de fluidez supera un valor determinado al pasar por el orificio de la boquilla a temperatura constante, se producirán grietas transversales evidentes en la superficie fundida, denominadas fractura de fusión, que deterioran la apariencia y las propiedades físicas de la pieza de plástico. Por lo tanto, al seleccionar polímeros con un alto índice de fluidez, se debe aumentar la sección transversal de la boquilla, el canal de alimentación y el puerto de alimentación, reducir la velocidad de inyección y aumentar la temperatura del material.
Rendimiento térmico y velocidad de enfriamiento
6.1 Los plásticos tienen diferentes propiedades térmicas, como calor específico, conductividad térmica y temperatura de deformación térmica. Los plásticos con alto calor específico requieren mucho calor para su plastificación, por lo que se recomienda seleccionar una máquina de moldeo por inyección con gran capacidad de plastificación. Los plásticos con alta temperatura de deformación térmica pueden tener un tiempo de enfriamiento corto y un desmoldeo precoz, pero se debe evitar la deformación por enfriamiento después del desmoldeo. Los plásticos con baja conductividad térmica se enfrían lentamente (como los ionómeros, que se enfrían muy lentamente), por lo que deben enfriarse completamente y se debe mejorar el efecto de enfriamiento del molde. Los moldes de canal caliente son adecuados para plásticos con bajo calor específico y alta conductividad térmica. Los plásticos con alto calor específico, baja conductividad térmica, baja temperatura de deformación térmica y enfriamiento lento no son propicios para el moldeo a alta velocidad, por lo que se deben seleccionar máquinas de moldeo por inyección adecuadas y mejorar la refrigeración del molde.
6.2 Diversos plásticos deben mantener una velocidad de enfriamiento adecuada según el tipo, las características y la forma de las piezas. Por lo tanto, el molde debe estar equipado con un sistema de calentamiento y enfriamiento según los requisitos de moldeo para mantener una temperatura específica. Cuando la temperatura del material aumenta la del molde, este debe enfriarse para evitar que la pieza se deforme después del desmoldeo, acortar el ciclo de moldeo y reducir la cristalinidad. Cuando el calor residual del plástico no es suficiente para mantener el molde a una temperatura determinada, este debe estar equipado con un sistema de calentamiento para controlar la velocidad de enfriamiento, garantizar la fluidez, mejorar las condiciones de llenado o controlar el enfriamiento lento de la pieza, evitar un enfriamiento desigual dentro y fuera de piezas de plástico de paredes gruesas y aumentar la cristalinidad. Para piezas con buena fluidez, gran área de moldeo y temperatura desigual del material, se puede utilizar calentamiento o enfriamiento alternado, o bien, calentamiento y enfriamiento local al mismo tiempo, según las condiciones de moldeo de la pieza. Por esta razón, el molde debe estar equipado con un sistema de calentamiento o enfriamiento correspondiente.
Higroscopicidad
Los plásticos contienen diversos aditivos que les confieren diferente afinidad con el agua. Por lo tanto, se pueden dividir, a grandes rasgos, en dos tipos: los que absorben la humedad y se adhieren al agua, y los que no la absorben y no se adhieren fácilmente a ella. El contenido de agua del material debe controlarse dentro del rango admisible; de lo contrario, el agua se gasificará o se hidrolizará a altas temperaturas y presiones, lo que provocará la formación de burbujas en la resina, reducirá su fluidez y deteriorará su aspecto y sus propiedades mecánicas. Por lo tanto, los plásticos higroscópicos deben precalentarse según los requisitos, utilizando métodos y especificaciones de calentamiento adecuados para evitar la reabsorción de humedad durante su uso.
Tamaño de la caja de plástico para rotación
Caja de rotación de 3# 350*260*125 Caja de rotación de 18# 840*625*450
Caja de rotación de 4# 410*305*145 Caja de rotación de 19# 605*415*307
Caja de rotación de 5# 480*350*170 Caja de rotación de 20# 600*395*430
Caja de rotación de 6# 540*420*240 Caja de rotación de 21# 378*243*100
Caja de rotación de 7# 660*400*145 Caja de rotación de 22# 553*412*260
Caja de rotación de 8# 540*420*300 Caja de rotación de 23# 525*365*205
Caja de rotación de 9# 540*430*380 Caja de rotación de 24# 600*300*210
Caja de rotación de 10# 600*500*350 Caja de rotación de 25# 520*380*170
Caja de rotación de 11# 705*560*380 Caja de rotación de 26# 520*380*170
Caja de rotación de 12# 475*353*320 Caja de rotación de 27# 450*255*126
Caja de rotación de 13# 600*500*400 Caja de rotación de 28# 443*300*113
Caja de rotación de 14# 610*417*120 Caja de rotación de 29# 500*320*178
Caja de rotación de 15 lb 605 x 415 x 244 Caja de rotación de 30 lb 480 x 352 x 220
Caja de rotación de 16# 600*500*300 Caja de rotación de 31# 525*365*262
Caja de rotación de 17# 707*453*175 Caja de rotación de 32# 550*365*165
Nueva caja de facturación n.° 15 600*500*150 Caja de facturación n.° 33 480*315*140
Bienvenidos a consultar y negociar.
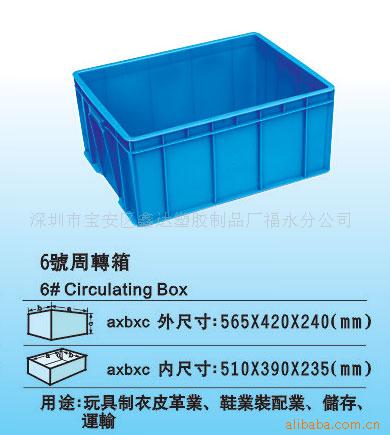
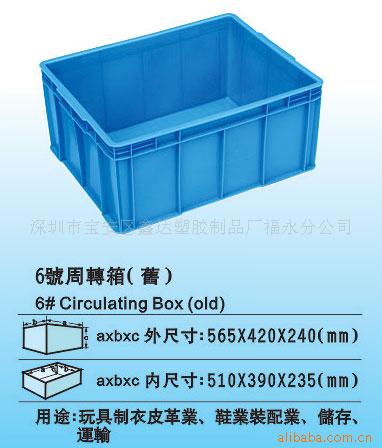
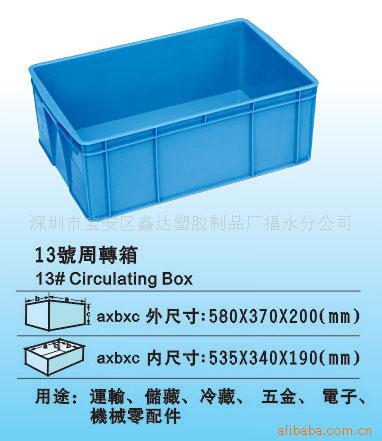
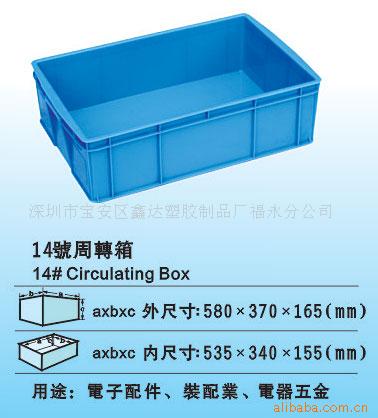
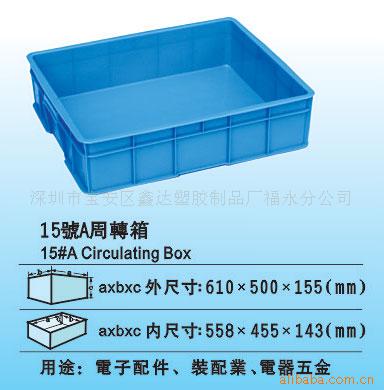
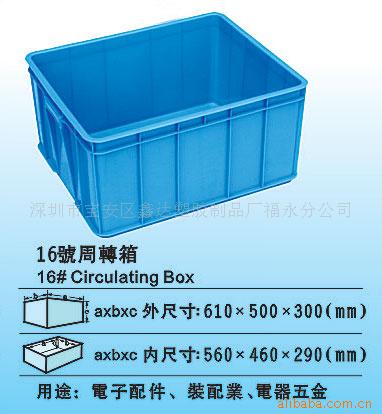
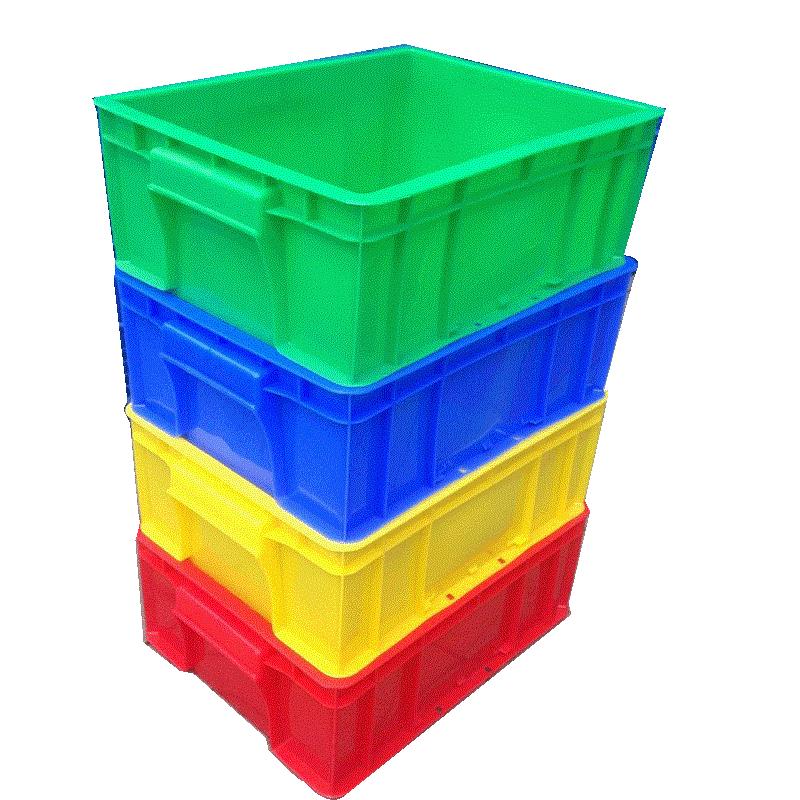
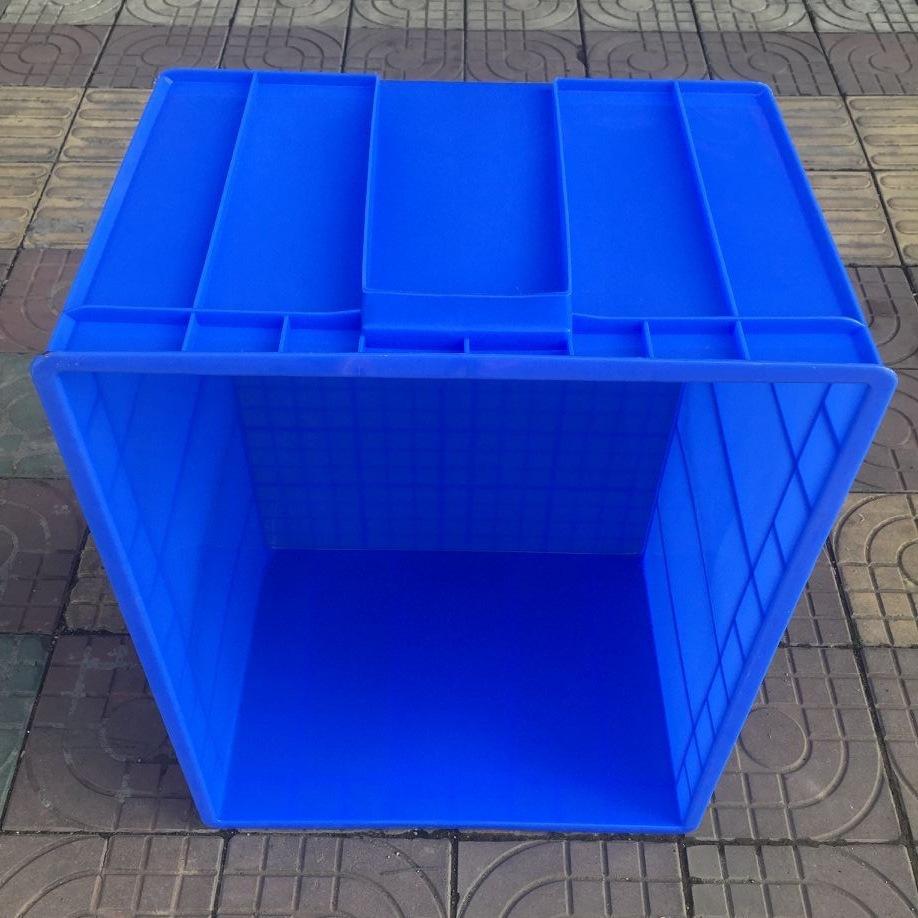
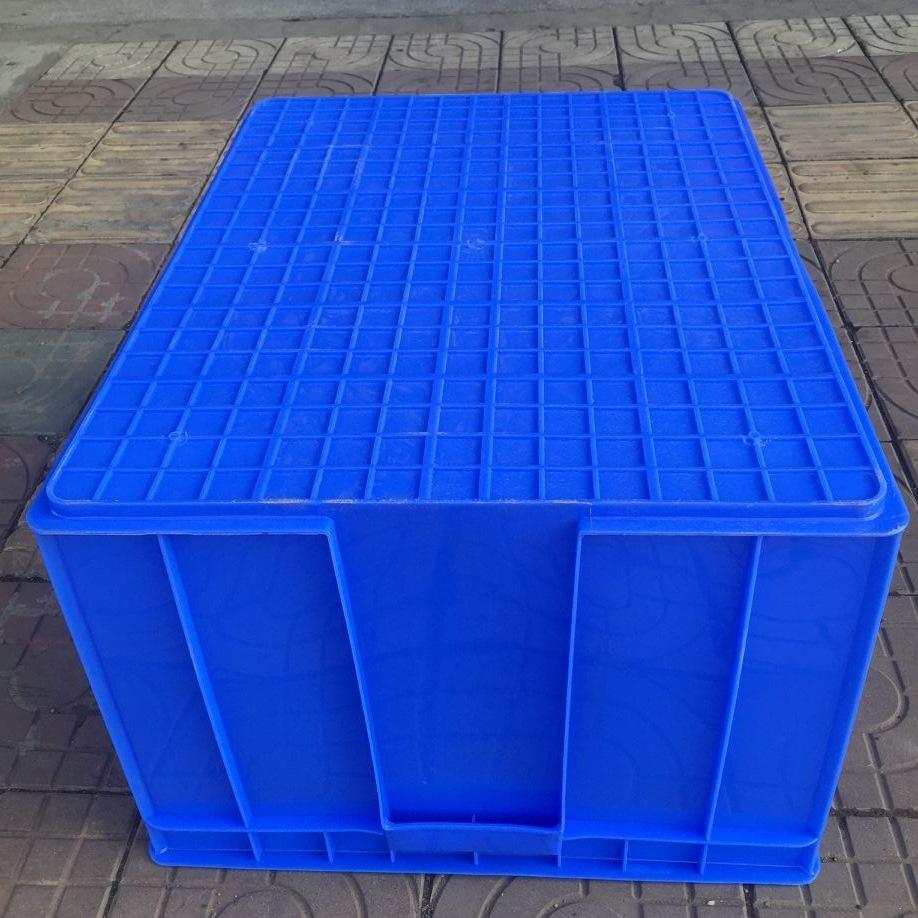
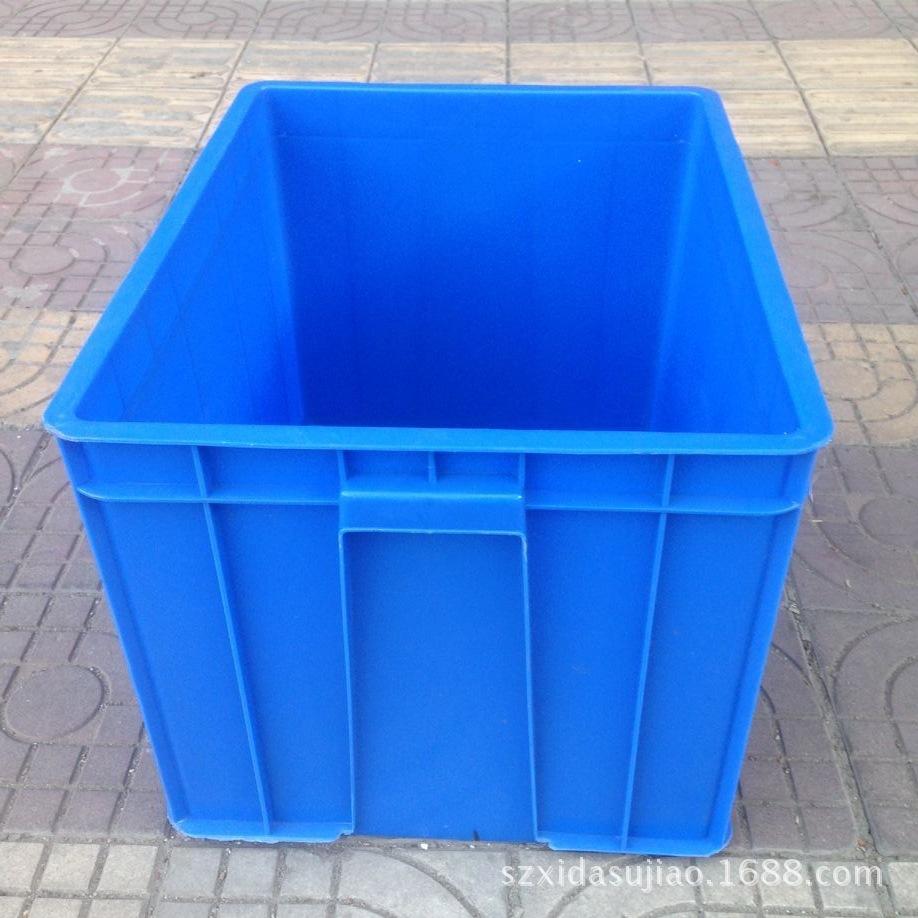
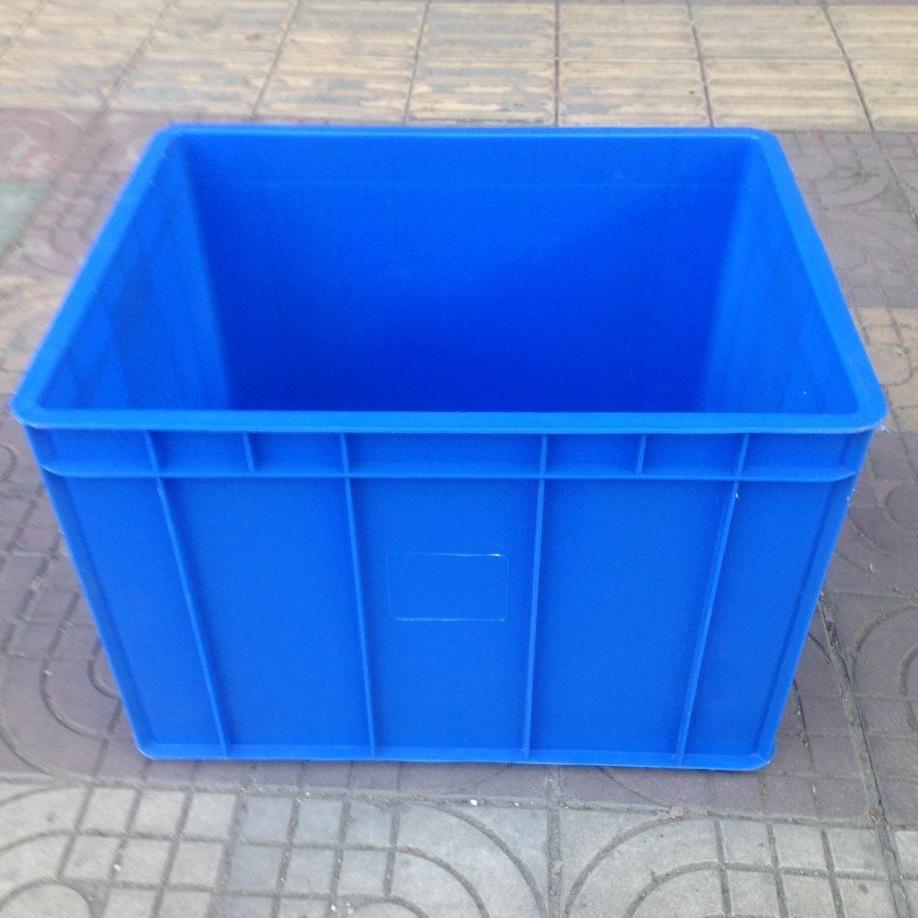
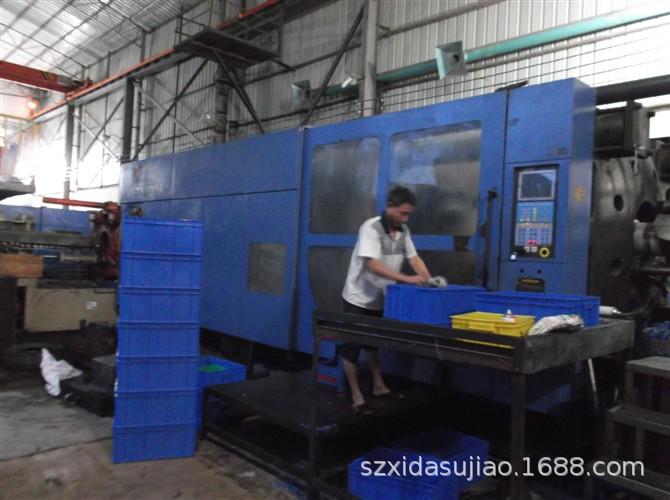
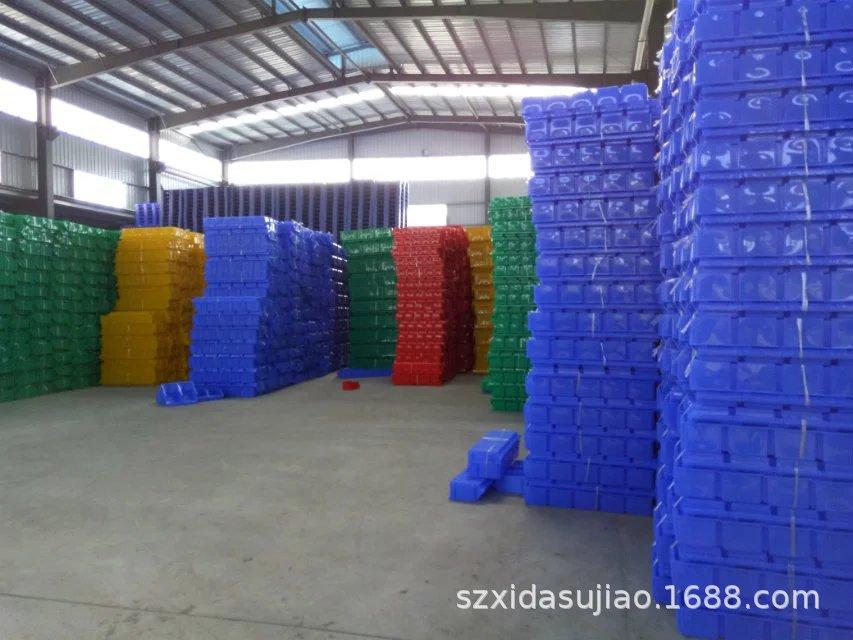